Racking Inspection Frequency: How Often Should You Inspect?
Table of ContentsConducting A Diy Racking Inspection: Pros, Cons, And ConsiderationsThe Importance Of Regular Racking Inspections In Preventing AccidentsRacking Protection And Damage Prevention: Tips And TricksOccupational Health And Safety InspectionsRacking Safety: How To Create A Culture Of PreventionWarehouse Safety Inspection Checklist
Regardless of exactly how well conducted, an evaluation will only be rewarding if the problems kept in mind by the group are meticulously checked out and also proper corrective activity is taken. The coverage and the ability levels of the people offered this responsibility will differ from one company to the following, but it is necessary to bear in mind the following factors when designating duty for examining examination reports.A minimum of one of the persons in charge of assessing inspection reports must have the authority to take or establish the essential rehabilitative procedures and to delegate that authority, as proper. Particular concerns may call for the point of view of a specialist, such as an engineer or a commercial hygienist. It is essential to inform those carrying out the examinations of any follow-up procedures that are to be taken, in order to enhance their inspiration.
It is equally as important to ensure that those that are in charge of doing evaluations obtain prompt feedback. Plainly, if there is no feedback or demonstration of interest, they will promptly end that assessments are a meaningless workout. Information acquired from normal assessments must be subject to a thorough evaluation in order to identify which areas are in demand of basic rehabilitative actions, as well as to recognize patterns as part of the efficiency bookkeeping program.
Racking Safety: How To Create A Culture Of Prevention
Any person in charge of bring out work location health and wellness and security assessments, specifically work location health as well as safety committee participants as well as representatives, will locate it beneficial.
Office evaluations aid protect against occurrences, injuries and ailments. With a vital assessment of the work environment, evaluations assist to recognize and tape dangers for corrective action. Health and wellness committees can aid strategy, conduct, record and also display assessments. Normal work environment assessments are an essential part of the general occupational wellness as well as safety program as well as administration system, if present.
g., design controls, administrative controls, policies, treatments, personal safety equipment) satisfy regulatory as well as administration system needs Preparation is crucial for an efficient examination. Every examination has to examine who, what, where, when and how. Pay particular attention to things that are or are more than likely to become hazardous or unhealthy problems due to stress and anxiety, wear, influence, resonance, warmth, corrosion, chain reaction or misuse.
Optimizing Safety In Warehouses With Data-driven Insights
Look at all workplace components the people, the setting, the devices, the products, and the procedure. Tools includes equipment, devices, and also device for creating an item or a solution, as well as safety and security tools as well as personal protective devices (PPE) that might be required.
Process involves exactly how the worker engages with the various other components in a series of tasks or procedures. Dangers can take place as a result of hazardous workplace problems and also methods involving the office elements. Kinds of work environment threats consist of: Security risks such as those caused by poor equipment guards, dangerous power (mechanical, electric, gravitational, pneumatically-driven, and so on), cars, machinery , devices , absence of autumn defense , confined rooms , and home cleaning .
Chemical dangers triggered by a strong, liquid, vapour, gas, dust, fume. or haze. Ergonomic hazards brought on by inappropriate work techniques, inaccurate manual material handling , and also inadequately designed workstations, tools, and also devices. These location physiological (recurring and powerful motions, awkward stances, overloading) and also emotional (workload, time stress) demands on the employee that can bring about musculoskeletal injuries.
Demystifying Palettier Cnesst Regulations For Warehouse Operators
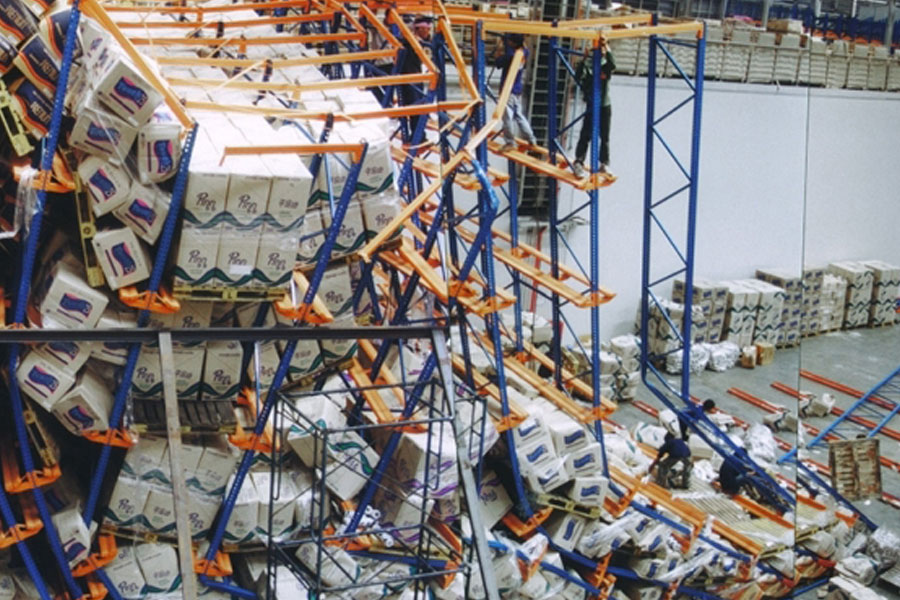
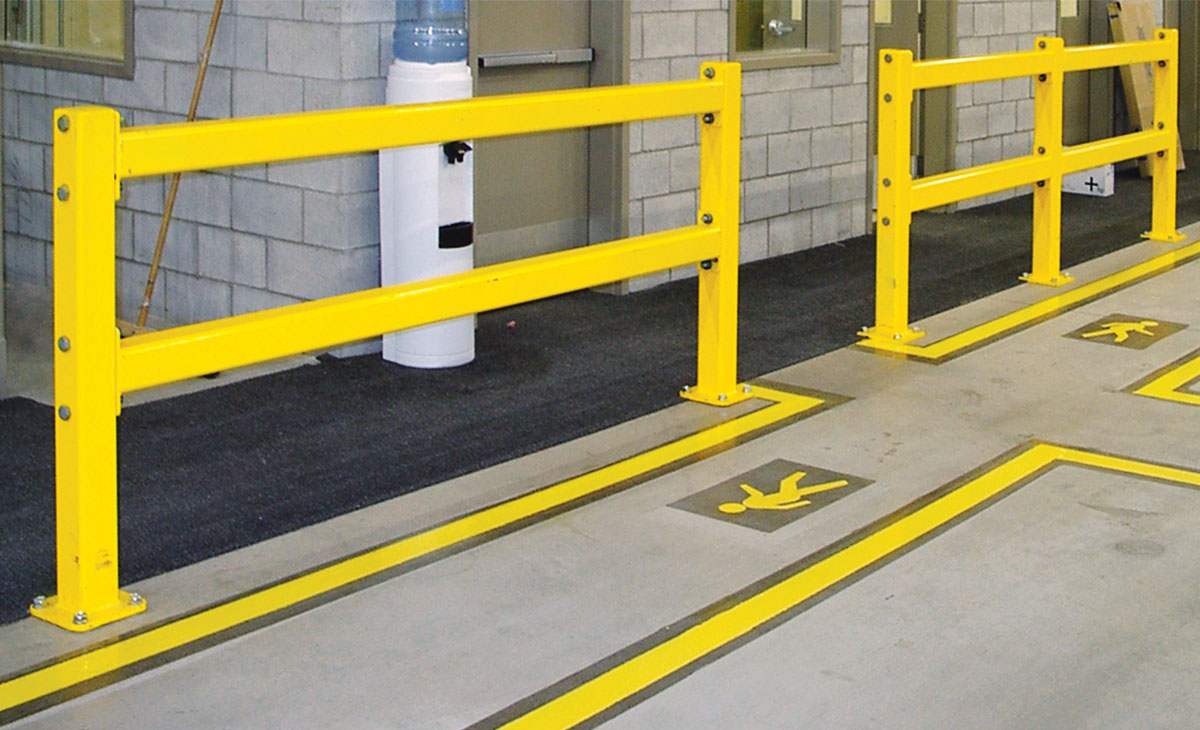
Read job location records to come to be familiar with the threats of the equipment. Be conscious of any kind of design security controls called for to safely run the equipment.
Maximizing Racking Protection With Strategic Planning
Examine that all harmful products are identified appropriately according to Workplace Hazardous Products Details System (WHMIS ) demands. These records consist of workplace plans, regulations and also laws, procedures, secure work techniques, emergency response plans, records, as well as documents. Recognizing with the regular risk-free operating conditions for the location can aid examiners to recognize risky discrepancies.
Do not permit the examination group to come to be so aim on noting the information provided in the list that it misses other hazardous conditions. Refer to the associated papers for example lists that you can make use of as a guide to establish a list that is customized for your work environment.
They additionally reveal what an earlier examination team focused on and what areas it did not evaluate. Do not just read this repeat or duplicate previous evaluation results. Use the older examination reports to assist try to find concerns, and after that establish whether recommendations were applied. Note if the adjustments have worked.
Innovative Solutions For Safety In Warehouses
Prior to doing an office assessment, assessors must come to be aware of any possible wellness and safety issues or patterns determined through other types of reports. The complying with defines various other sorts of reports: Recurring examinations Threat reports Occurrence and also examination reports Evaluation compliance orders Pre-operation checks Pre-start engineering health and wellness testimonials Work risk evaluation (JHA) Periodic inspections (preventative maintenance) Tracking device information (work-related health) Interior and also exterior audits Health and wellness summaries: you can check here Supervisors and employees ought to conduct recurring inspections as part of their job duties.